CNC milling machines, especially 3-axis desktop models, are widely used in modern manufacturing for precise and efficient machining of metal parts. However, like all machinery, they can experience common faults over time, which can negatively impact machining accuracy and production efficiency. Therefore, identifying and resolving these issues in a timely manner is crucial for maintaining the machine's stable operation. This article will analyze the common faults in desktop 3-axis CNC milling machines and provide corresponding solutions.
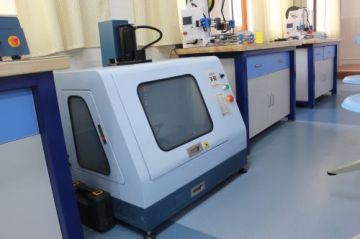
1. Positional Error
Symptom: Positional error refers to the deviation between the actual position of the machine and the target position during the positioning process. This fault typically manifests as inaccuracies in the dimensions or shape of the machined parts.
Possible Causes:
Loose Mechanical Components: If critical parts such as the guide rails, bearings, or other connections are loose, it can lead to inaccurate positioning.
Damaged Bearings: Bearings are key components in the machine's motion system. If they wear out, become stuck, or fail, the precision of motion can be compromised, leading to positional errors.
Encoder Malfunction: Encoders provide feedback on the position of each axis. If the encoder malfunctions or the signal is interfered with, it can result in errors.
Servo System Abnormalities: Problems with the servo motor control system, particularly under high load or acceleration conditions, can lead to positioning errors.
Solutions:
Regularly check the machine’s mechanical structure to ensure that all components are securely tightened, especially the guide rails and ball screws.
Inspect and replace worn or damaged bearings to ensure smooth operation.
Test the encoder signals and recalibrate or replace faulty encoders if necessary.
Inspect the servo system for any faults, ensuring the drive motors receive normal control signals and are not overloaded or losing steps.
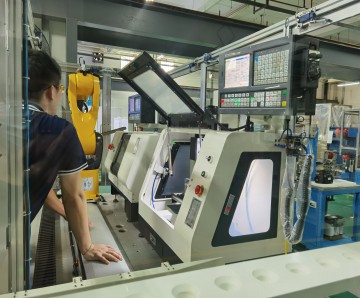
2. Unstable Feedrate
Symptom: Unstable feedrate refers to fluctuations in the feed speed, or the occurrence of stalling or jerking at certain positions. This problem affects the surface quality of the workpiece and may even cause machining failure.
Possible Causes:
Faulty Drive Motors: Insufficient motor power or malfunctioning drive modules can cause unstable feedrates, especially if stepper or servo motors are damaged.
Feed System Malfunctions: Problems in the feed transmission system (e.g., loose ball screws, slipping drive belts) can lead to unstable feeding, particularly under heavy loads.
Control System Issues: If there are abnormalities in the CNC system’s control signals or incorrect parameter settings, the feedrate may fluctuate.
Power Supply Problems: Instability in the power supply or voltage fluctuations can cause the motors to run unevenly, resulting in feedrate instability.
Solutions:
Inspect the motors for faults and replace or repair them if necessary.
Check the feed transmission system for issues such as looseness in ball screws, guide rails, and couplings, and ensure that the drive belts are properly tensioned.
Review and adjust the CNC system’s feed control parameters to ensure they match the processing requirements.
Use a stable power supply to prevent voltage fluctuations and install voltage regulators if necessary.
3. Cutting Vibration
Symptom: Cutting vibration occurs when the machine experiences oscillations during the milling process. This can manifest as tool chatter, rough surface finishes, and dimensional inaccuracies. Cutting vibration not only affects machining precision but also shortens tool life.
Possible Causes:
Improper Tool Selection: If the tool material, geometry, or cutting edge configuration is not suitable for the workpiece material or machining conditions, cutting forces may increase, leading to vibration.
Inappropriate Cutting Parameters: Incorrect settings for cutting depth, speed, or feed rate can result in excessive cutting forces, leading to vibration.
Unstable Fixtures: If the fixture lacks sufficient rigidity or is improperly clamped, vibrations can transfer between the workpiece and the tool, affecting machining quality.
Poor Machine Rigidity: Desktop CNC milling machines tend to have lower rigidity compared to larger machines. External disturbances or cutting forces can induce vibrations.
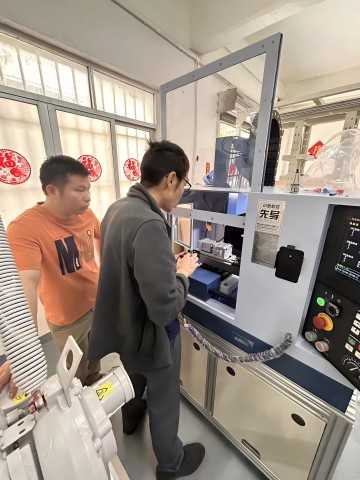
Solutions:
Select the appropriate cutting tool based on the material and machining conditions. Avoid using worn-out tools.
Optimize cutting parameters to reduce excessive cutting forces, and avoid using excessive cutting depth or low cutting speeds.
Ensure that the workpiece is securely clamped with stable fixtures to prevent movement during machining.
Check the machine’s rigidity to make sure that all parts are securely connected and tightened to minimize vibrations caused by machine flexibility.
4. Servo System Loss of Steps
Symptom: Loss of steps in the servo system refers to a situation where the servo motor fails to follow the desired motion trajectory, leading to positioning errors and reduced machining accuracy.
Possible Causes:
Overload of Servo Motors: If the machine encounters excessive load during machining, the servo motors may become overloaded, leading to a loss of steps.
Encoder Signal Interference: If the feedback signal from the encoder is inaccurate or interfered with, the servo motor may receive incorrect position data, resulting in step loss.
Incorrect Control System Settings: Incorrect parameters in the CNC system, such as high acceleration or speed limits, may cause the motor to lose steps.
Solutions:
Regularly check for overloading conditions and ensure that the servo motors operate within their specified load limits.
Inspect the encoder and feedback wiring for any signal interference, and eliminate any electrical noise that could disrupt the feedback signals.
Adjust the CNC system’s servo parameters to optimize motor acceleration, speed, and other settings to prevent step loss.
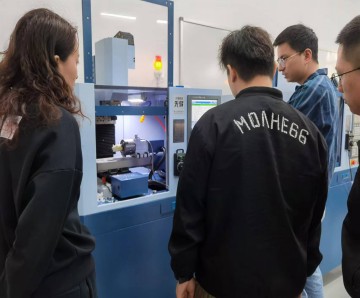
Conclusion
Desktop 3-axis CNC milling machines are highly efficient and accurate tools for precision machining, but like all equipment, they are prone to various faults over time. Regular maintenance, timely fault detection, and appropriate corrective measures are essential for extending the life of the machine and ensuring continuous production. By addressing common faults such as positional errors, unstable feedrates, cutting vibrations, and servo system loss of steps, manufacturers can maintain the stability and reliability of their CNC milling machines, ensuring high-quality machining and optimal performance.