As modern manufacturing demands greater precision and efficiency, 5-axis CNC machines have become widely used in industries such as aerospace, automotive, and mold manufacturing due to their powerful machining capabilities and flexibility. However, during high-precision machining, it is crucial to address cooling and lubrication issues to avoid overheating of the workpiece or excessive tool wear, which can significantly affect both the quality and efficiency of the process.
This article will explore the key cooling and lubrication challenges in 5-axis CNC machining, emphasizing how to optimize these processes to enhance machining efficiency and extend tool life.
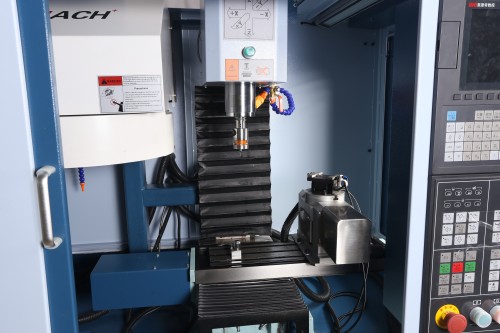
1. Features of 5-Axis CNC Machining
Compared to traditional 3-axis machines, 5-axis CNC machines offer superior precision and the ability to machine more complex shapes. By controlling two additional rotational axes, 5-axis machines can achieve intricate tool paths, enabling the production of fine and complex components. This makes them particularly useful in industries such as aerospace, automotive, and medical device manufacturing.
However, the machining environment of a 5-axis CNC machine typically involves high-speed cutting and high heat generation, especially during deep-hole drilling, precision contouring, or other complex operations. Cooling and lubrication become essential to managing these conditions effectively. Proper use of coolant and lubricants can prevent thermal deformation of the workpiece and reduce tool wear, ensuring the desired machining precision and improving overall efficiency.
2. The Role of Cooling and Lubrication
Cooling and lubrication are vital for addressing two main issues during 5-axis CNC machining: excessive heat and tool wear.
Cooling Function
Lowering Cutting Temperatures: During high-speed cutting, the cutting area generates substantial heat. Without effective cooling, excessive temperatures can lead to thermal expansion of the workpiece and tool, resulting in dimensional inaccuracies. Coolant applied directly to the cutting area helps absorb heat and lowers the temperature, ensuring machining precision.
Preventing Heat Buildup: Excessive heat can soften tool materials, reducing tool hardness and wear resistance. Cooling fluids help prevent such heat accumulation, maintaining tool integrity and reducing the risk of premature tool failure.
Lubrication Function
Reducing Friction and Wear: Tool wear is mainly caused by friction between the cutting tool and the workpiece. Lubrication helps create a thin lubricating film between the tool and workpiece, reducing direct contact and lowering the friction coefficient. This results in a longer tool life and more stable cutting conditions.
Improving Cutting Efficiency: Lubricants reduce cutting forces and cutting temperatures, which in turn lowers the power consumption of the machine and improves overall machining efficiency.
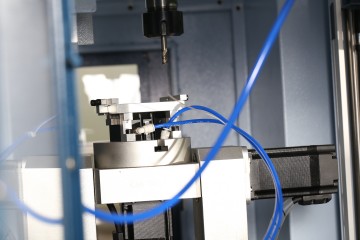
3. Cooling and Lubrication Systems in 5-Axis CNC Machining
Given the complexity of the cutting zone in 5-axis CNC machining, the design of cooling and lubrication systems must consider the machine's structure, toolpath, and the characteristics of the workpiece. Below are common cooling and lubrication methods used in 5-axis CNC machining.
Internal Cooling System
Internal Tool Cooling Channels: Some high-end 5-axis CNC machines are equipped with an internal cooling system that directs coolant through channels inside the tool. This method ensures that coolant is delivered directly to the cutting edge, which helps maintain a consistent temperature and prevents overheating during cutting.
Advantages: Internal cooling improves cooling efficiency because the coolant directly contacts the cutting area, reducing heat buildup.
Disadvantages: Internal cooling requires specialized tools with internal channels, and it places higher demands on the coolant flow rate and pressure.
External Cooling System
Spray Cooling: External spray cooling involves spraying coolant directly onto the cutting zone from nozzles placed near the spindle or workpiece. This method is common in many 5-axis CNC machines and effectively cools the cutting area, albeit less efficiently than internal cooling.
Advantages: Spray cooling is simpler in design and can still provide effective cooling for most machining operations.
Disadvantages: As coolant does not contact the tool directly, cooling efficiency is lower compared to internal cooling methods. It may not be suitable for applications with stringent temperature control requirements.
Air-Mist Cooling and Lubrication
Air-Mist Cooling: Air-mist systems combine compressed air with coolant to create a fine mist that is directed onto the cutting zone. This method helps reduce coolant consumption while still providing adequate cooling.
Air-Mist Lubrication: Air-mist lubrication involves using fine misted lubricants to reduce friction. The air helps distribute the lubricant evenly across the cutting area, ensuring consistent lubrication even in complex tool paths.
Advantages: Suitable for complex or precision machining, as it reduces tool wear and prolongs tool life.
Disadvantages: Requires a reliable air source and precise control of coolant and lubricant flow, which can increase initial setup costs.
Dry Cutting Technology
Dry Cutting: In some cases, 5-axis CNC machines can perform dry cutting, where no coolant or lubrication is used. This method relies solely on the material properties of the tool and workpiece, as well as cutting forces, to perform the machining operation.
Advantages: Reduces environmental impact by eliminating coolant disposal issues and lowers maintenance costs associated with coolant systems.
Disadvantages: Dry cutting can lead to excessive tool wear and high temperatures, making it unsuitable for high-precision or high-volume machining operations.
4. Choosing and Optimizing Coolant and Lubrication
Selection of CoolantChoosing the right coolant is essential for optimizing performance in 5-axis CNC machining. Common types include water-soluble coolants and oil-based coolants. Water-soluble coolants are typically used for most general machining tasks, while oil-based coolants are better suited for high-load or high-temperature cutting environments.
Lubricant SelectionChoosing the right lubricant ensures longer tool life and reduces cutting forces and temperatures. The selection of lubricant depends on the machining material, cutting conditions, and the specific type of operation. Key properties to consider include viscosity, anti-oxidation performance, and extreme pressure resistance.
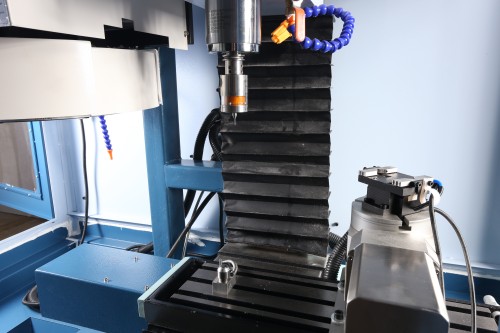
5. Conclusion
High-precision 5-axis CNC machining relies heavily on effective cooling and lubrication strategies. To optimize the cooling and lubrication systems, factors such as the characteristics of the workpiece, tool material, and cutting parameters must be carefully considered. Proper cooling and lubrication not only extend tool life but also reduce thermal deformation, enhance cutting efficiency, and improve overall machining accuracy. With the continuous advancement of technology, new and more effective cooling and lubrication techniques will be integrated into 5-axis CNC machines, further expanding their potential in high-precision manufacturing applications.