The Mini Metal Sanding Machine is a versatile, compact tool that plays a key role in modern manufacturing, particularly for small, precision parts. It combines high accuracy with flexibility, allowing for a range of sanding operations like external cylindrical, internal cylindrical, and surface sanding. This article explores the Mini Metal Sanding Machine's functionality and how to choose the right sanding method based on the shape, size, and requirements of the workpiece.
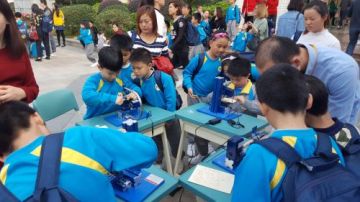
The Mini Metal Sanding Machine is designed for precision sanding, especially for smaller workpieces. Despite its compact size, it offers versatility and can handle various sanding tasks efficiently. The basic operating principle is that a high-speed rotating sanding wheel removes material from the workpiece surface, achieving the desired dimensions and surface finish.
Key components include:
Spindle System: Supports the sanding wheel and provides high-speed rotation.
Feed System: Adjusts the relative movement between the wheel and workpiece.
Workpiece Clamping System: Ensures that the workpiece is securely held during sanding.
Sanding Wheel System: Includes the wheel, its holder, and adjustments for wheel speed and feed.
Understanding the machine’s components is crucial for mastering its use and ensuring precise sanding operations.
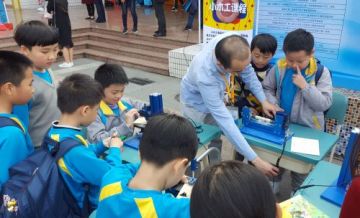
2. Common Sanding Methods and Their Applications
External Cylindrical Sanding
External cylindrical sanding is used to process the outer cylindrical surfaces of workpieces, such as shafts, gears, and bearing housings. This method achieves high precision, particularly for round parts that require tight tolerances and smooth finishes.
Teaching Focus: The key to successful external cylindrical sanding is selecting the correct sanding wheel, adjusting the wheel speed, and controlling feed rates. Students should learn how to monitor these variables to achieve the desired roundness and surface quality.
Practical Application: Instructors should demonstrate how to set up the machine, adjust the wheel and feed rates, and check the workpiece for dimensional accuracy.
Internal Cylindrical Sanding
Internal cylindrical sanding is used for machining internal holes, such as those in bearings or bushings. This type of sanding requires precise wheel selection and careful feed control to achieve accurate hole diameters and smooth surfaces.
Teaching Focus: Students need to learn how to select the correct sanding wheel size and adjust the feed rate for internal sanding. Instructors should also demonstrate proper workpiece clamping methods to ensure accurate machining of inner surfaces.
Practical Application: Students should practice sanding small internal diameters and adjusting parameters for precision.
Surface Sanding
Surface sanding is used to smooth flat surfaces of workpieces, such as plates, molds, or baseplates. It requires careful control of feed speed, wheel type, and contact area to achieve the desired surface finish.
Teaching Focus: In surface sanding, instructors should emphasize controlling the sanding path and feed rates to ensure uniform material removal. Students must also learn how to adjust for flatness and desired surface roughness.
Practical Application: By working on flat parts, students can practice setting up the sanding wheel, adjusting the workpiece, and ensuring smooth, even sanding.
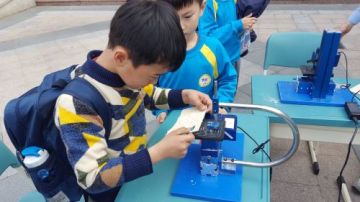
Cutting Sanding
Cutting sanding is a hybrid method that combines sanding with cutting processes. This method is often used for hard materials, such as carbide, that require high removal rates while maintaining precision.
Teaching Focus: Students should learn how to balance sanding and cutting speeds to efficiently process tough materials without sacrificing surface quality or dimensional accuracy.
Practical Application: Instructors can guide students in setting up the machine for cutting sanding, focusing on adjusting the depth of cut and feed rates for tough materials.
3. Choosing the Right Sanding Method
Choosing the correct sanding method based on the workpiece's shape, size, and processing requirements is key to achieving optimal results. Below are some guidelines for selecting the right sanding method:
Small Precision Workpieces
For small, precise parts, external and internal cylindrical sanding are commonly used. These workpieces often require high surface finish and dimensional accuracy, which the Mini Metal Sanding Machine is well-suited for.
Complex Shaped Workpieces
For workpieces with intricate shapes or multiple features, a combination of external and surface sanding is ideal. Students should be taught how to design fixtures to hold complex parts securely and select appropriate sanding parameters for the task.
High Hardness Materials
For hard materials, such as carbide or tool steels, cutting sanding or a combination of cylindrical sanding methods is often used. These materials require careful wheel selection and precise adjustments to minimize wear and heat buildup.
4. Common Sanding Problems and Solutions
During training, students should also be prepared to handle common sanding issues that arise during operations. These problems include:
Excessive Sanding Force: This can lead to workpiece deformation or rapid wheel wear. It can be solved by adjusting feed rates, reducing wheel speed, or using finer sanding wheels.
Poor Surface Finish: This can result from using coarse wheels or excessive feed rates. Students should learn how to fine-tune wheel selection, feed speeds, and pressure to achieve a smooth surface.
Workpiece Overheating: Overheating occurs when too much friction generates excessive heat, affecting material properties. Using coolant and adjusting feed rates can help reduce heat buildup during sanding.
By understanding these common issues and their solutions, students will be better equipped to troubleshoot problems in real-world sanding applications.
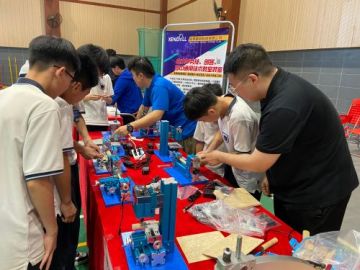
5. Practical Training and Assessment
Hands-on training is crucial for mastering the operation of the Mini Metal Sanding Machine. Students need to practice using the machine in a controlled environment to develop their skills.
Demonstration and Imitation: Instructors should first demonstrate the correct operation of the sanding machine, then allow students to replicate these steps.
Practical Tasks: Tasks should progressively increase in complexity, from simple cylindrical sanding to more complicated surface sanding or internal sanding operations.
Evaluation and Feedback: After each practical session, instructors should assess students based on their workpiece’s dimensional accuracy and surface quality. Constructive feedback helps students identify areas for improvement.
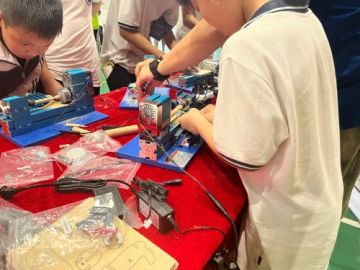
6. Conclusion
The Mini Metal Sanding Machine is a crucial tool in precision manufacturing, especially for small parts. It offers flexibility and accuracy across various sanding methods, from external and internal cylindrical sanding to surface sanding and cutting sanding. In teaching, it is important to combine theoretical knowledge with practical training to help students understand the machine’s functions, troubleshoot common issues, and select the right sanding methods based on workpiece specifications.
For related products, please click the link for more details.:https://www.xendolltools.com/product/Metal_Sanding_Machine.htmlXendoll has over 20 years of experience in manufacturing universal metalworking machines for teaching purposes, with single-piece orders available. Feel free to contact us for inquiries!