In modern manufacturing and rapid prototyping, desktop 3-axis CNC machines have become increasingly popular due to their compact size and high efficiency. These machines are favored by small businesses, educational institutions, and hobbyists for their cost-effectiveness and ability to provide precise machining. However, machining accuracy on desktop machines can be affected by several factors. How to improve the precision of these machines is a key concern for many users. This article explores the advantages and disadvantages of desktop 3-axis CNC machines, analyzes the factors affecting their accuracy, and provides methods for improving precision.
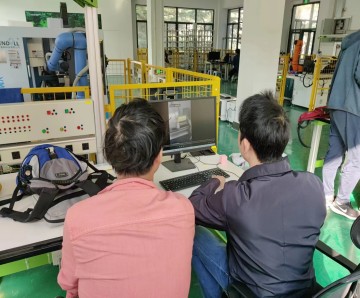
I. Advantages of Desktop 3-Axis CNC Machines
Low Cost, High Value for Money
Desktop 3-axis CNC machines are significantly more affordable than their industrial counterparts, making them an ideal choice for small businesses, makers, and hobbyists. In addition to lower purchase costs, desktop CNC machines generally have lower maintenance and operational costs due to their smaller size and simpler construction. This makes them an attractive option for small-scale projects and startups with limited budgets. Furthermore, their low power consumption helps reduce long-term operating expenses.
Space-Saving and Suitable for Small Environments
The compact size of desktop CNC machines makes them suitable for environments with limited space, such as small workshops, home studios, or educational labs. Unlike large industrial machines, desktop CNC machines require very little floor space, making them ideal for urban areas or places where space is a premium.
Ease of Use, Ideal for Education and Entry-Level Learning
Most desktop CNC machines come with intuitive control panels and user-friendly software interfaces, making them easy to operate, even for beginners. Many machines are compatible with popular CAD/CAM software, streamlining the design-to-production workflow. Because of their simple operation, desktop machines are particularly beneficial in educational settings where students or newcomers are learning CNC technology and machining principles.
High Precision for Small Parts
Despite their smaller size, desktop 3-axis CNC machines are capable of delivering high precision, typically achieving tolerances of 0.01 mm or better. This makes them ideal for small part machining, rapid prototyping, and custom manufacturing. The ability to produce fine, accurate parts makes them invaluable for product design and testing, as well as low-volume production runs.
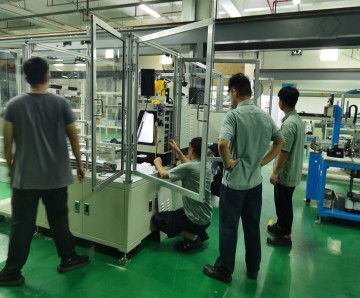
II. Disadvantages of Desktop 3-Axis CNC Machines
Limited Work Envelope
The most significant limitation of desktop CNC machines is their small working area. The reduced size of the machine’s work envelope limits the dimensions of parts that can be machined, making these machines unsuitable for large or complex parts. This is a key disadvantage when larger workpieces or high-volume production are required.
Lower Rigidity and Stability
Desktop CNC machines are generally constructed from lighter materials, which results in lower rigidity compared to industrial-sized machines. This can lead to issues with vibration and tool deflection, especially when machining harder materials or performing high-speed operations. These factors can negatively impact machining accuracy and surface finish, particularly during more demanding tasks.
Reduced Cutting Force
Due to their smaller motors and lighter construction, desktop CNC machines typically have less cutting force compared to larger industrial machines. As a result, they may struggle with tougher materials such as steel or high-strength alloys, limiting their capabilities in certain machining applications.
Slower Cutting Speeds
Desktop CNC machines usually have lower spindle speeds and feed rates compared to larger, more powerful machines. While this slower pace can sometimes benefit precision, it can also result in longer machining times, which may be inefficient for mass production or time-sensitive projects.
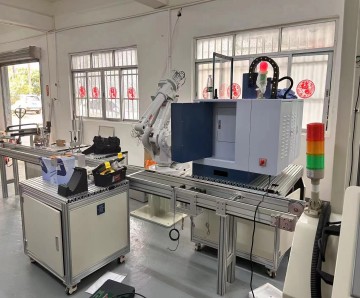
III. How to Improve the Precision of Desktop 3-Axis CNC Machines
Despite their limitations, desktop 3-axis CNC machines can still achieve excellent machining precision with the right setup and operational adjustments. The following are several methods to improve the machining accuracy of desktop CNC machines:
Regular Calibration
One of the most important steps to maintaining high precision is regularly calibrating the machine. This involves checking the alignment of the machine’s axes, ensuring the frame is square, and verifying the accuracy of the lead screws and linear guides. Routine calibration helps to correct any misalignments and ensure that the machine continues to operate within the required tolerances.
Use of High-Quality Components
The accuracy of desktop CNC machines can be significantly improved by upgrading key components such as lead screws, linear rails, and bearings. High-precision components can reduce backlash, minimize play, and improve the overall rigidity and stability of the machine, all of which contribute to better machining accuracy.
Upgrading to Closed-Loop Control Systems
Many desktop CNC machines use open-loop control systems with stepper motors, which can result in lost steps or inaccuracies. Upgrading to a closed-loop control system that uses encoders and feedback loops provides real-time monitoring and correction, ensuring more accurate and reliable motion control. This can significantly improve machining precision and system stability.
Optimizing Cutting Parameters
Choosing the correct cutting parameters—such as spindle speed, feed rate, and toolpath strategy—is essential for maximizing precision. Proper cutting speeds and feed rates reduce the likelihood of tool deflection and minimize the effects of vibrations. Slower, more controlled feeds often result in better surface finishes and higher accuracy during machining.
Stable Machine Setup and Environmental Control
Ensuring that the CNC machine is securely mounted on a rigid, stable surface is critical to minimizing vibrations during machining. Using a vibration-dampening base or pad can help prevent any unwanted flexing or movement during operations. Additionally, maintaining a stable operating environment—such as consistent temperature and humidity—can prevent material expansion or contraction, which may affect machining accuracy.
Tool Maintenance and Quality
The condition of the cutting tools plays a vital role in machining accuracy. Regularly inspecting and maintaining tools, replacing dull or damaged tools, and using high-quality tools suited for specific materials will reduce tool wear and deflection, leading to better surface finishes and improved precision.
Using Anti-Vibration Measures
Vibration can be a significant factor affecting machining precision. Using vibration-damping materials or anti-vibration tool holders can minimize tool chatter and deflection during the machining process. By reducing vibrations, these measures ensure that the machine operates with greater stability, thereby improving machining accuracy.
Enhanced Cooling and Lubrication
Proper cooling and lubrication during machining help reduce friction and heat buildup, which can distort parts and reduce accuracy. Using the appropriate coolant or lubricant for the specific material being machined not only extends tool life but also ensures more precise cuts, especially when dealing with harder materials.
Software Optimization
Optimizing CAM software settings can also play a crucial role in enhancing machining precision. Fine-tuning toolpaths, adjusting cutting strategies for material behavior, and optimizing machine motion profiles help reduce errors during the machining process, leading to more consistent and accurate results.
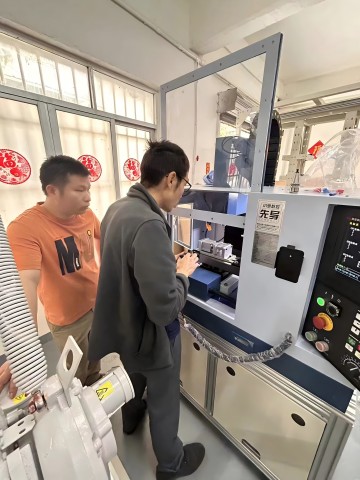
IV. Conclusion
Desktop 3-axis CNC machines provide an excellent, cost-effective solution for small part machining, rapid prototyping, and educational purposes. While they have limitations in terms of work envelope, rigidity, and cutting force, they can still produce high-quality, precise parts with the right setup and care. By focusing on regular calibration, upgrading key components, optimizing cutting parameters, and maintaining proper tool and environmental conditions, users can significantly improve the accuracy and performance of their desktop CNC machines. With these enhancements, desktop CNC machines remain a valuable tool for small-scale manufacturing, prototyping, and learning applications.